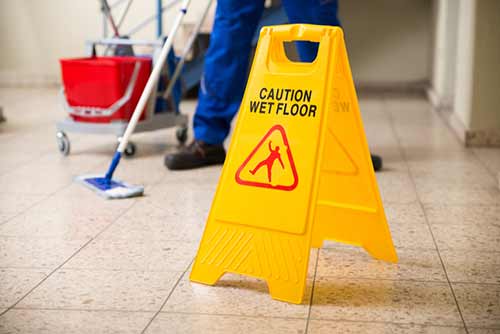
Heavy machinery, moving vehicles and hazardous chemicals and substances are just some of the reasons that industrial workplaces can be very dangerous environments for employers, employees and members of the public. Therefore, it
is essential to minimise all potential hazards to provide a safe and productive industrial workplace.
Hazards can range from accidental slips and falls, to burns from exposure to severely toxic chemicals and injuries from machinery. With so many hazards that can occur in industrial workplaces, it is important to be aware of these
and constantly refresh your rules, regulations, and checks to ensure maximum health and safety measures have been taken. This is especially vital as up to up to 2 million people a year are injured on the job due to failed hazard prevention and precautions.
With that in mind, here are the top 5 hazards to look out for in industrial environments...
Top 5 hazards to look out for in industrial workplaces
Hazards in the workplace vary according to industry and type of work being carried out. However, there are some hazards that are applicable to all workplaces. Identifying potential hazards in the workplace will help create a strong risk assessment to keep your employees safe. Below are some of the most common industrial hazards to help you identify risks in your own workplace.
Slips, trips and falls:
Slips, trips and falls are one of the most common accidents to occur in the workplace. According to the HSE (Health and Safety Executive), 40% of workplace injuries reported to them are due to slips, trips, and falls. Additionally, 95% of workplace accidents are due to unsafe behaviour, such as not putting appropriate measures in place to prevent slips, trips, and falls.
Ways of preventing this hazard:
- Implementing and regulating a set of specific rules for all employees to adhere to regarding falls in the workplace. This includes providing a compulsory safety briefing for any new employees, as well as regular refreshers
for existing employees.
- Putting mats and fitted matting systems in doorways to prevent mud, rain and other debris from being walked into areas where people may slip, trip or fall.
- Regularly maintaining and repairing flooring when required (including hard floors and carpets).
- Promptly cleaning any mess, including mopping up spills and clearing debris. A 'wet floor' hazard sign should be displayed when cleaning has been carried out, or to warn people if the area is not able to be cleaned immediately.
Contaminated clothing and workwear:
This is a huge risk in industrial workplaces due to the range of chemicals and substances you can be exposed to and these have varying levels of toxicity. Many activities carried out by industrial workers such as mining, can cause
such harmful substances to end up on your clothing, which can contaminate other area (such as the home).
Ways of preventing this hazard:
- Chemicals such as asbestos and hydrochloric acid can be highly toxic and damaging if they come into contact with human skin. Therefore, it is essential that you equip your staff with the correct protective workwear for their working environment.
- Your business should implement a rule that no one is permitted to leave the site with their work garments due to the risk of directly or indirectly spreading dangerous chemicals. This can cause unwanted exposure to oneself,
family and extended environment.
- Use a professional industrial laundering service, such as the one offered by phs Besafe to ensure your protective workwear is cleaned to the highest
standard to retain its compliance.
Stress and fatigue
Stress and fatigue can have a detrimental effect on employees' concentration levels and quality of work, particularly in industrial environments which often require workers to operate vehicles and heavy machinery,
as well as work long and unsociable hours. This can also be exceptionally dangerous if your employees are working with corrosive chemicals.
Ways of preventing this hazard:
- Let your workers have regular and substantial breaks. Make sure there is constant access to high quality water and food to prevent dehydration and keep energy levels high and reduce working hours and the time between shifts
where possible. These are all vital as the mental and physical health of staff should be a paramount concern in any business.
- Develop a wellbeing programme where workers are regularly checked up on to see how they are in terms of both their mental and physical health. This will enhance productivity, and strengthen the connection between employer and
employee.
Burns from chemicals and fires
Burns from chemicals and fires are extremely dangerous causing serious and lasting damage to employees and in many cases, even their death. You should not only prevent fires and exposure to corrosive chemicals from occurring, but
ensure your employees are adequately equipped if an incident were to occur.
Ways of preventing this hazard:
- Have an emergency action plan that all employees are informed of and ensure that first aid kits and other supplies (such as fire extinguishers) are easily available and in full working order. This will minimise the immediate damage.
- Having compliant and up-to-date fire alarms and smoke detectors are vital for discovering a fire and warning employees and visitors of its presence as soon as possible.
- At phs Besafe, we provide a range of protective workwear (such as flame resistant garments) to prevent your employees' from coming into direct contact with
corrosive chemicals and flames.
Poor visibility in low light environments
Poor visibility in low light environments can be extremely harmful as it reduces accuracy, which can increase the risk of life-threatening accidents. These include being hit by a moving vehicle or coming
into contact with dangerous machinery.
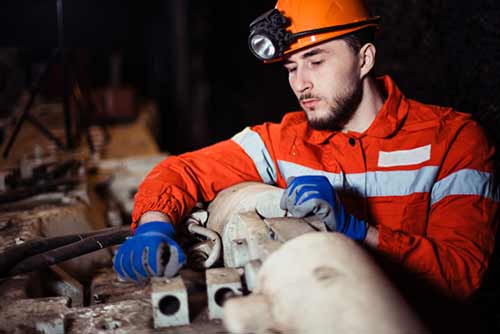
Ways of preventing this hazard:
- Provide high visibility workwear which will enable everyone to be seen and reduce accidents. At phs Besafe, our safety workwear is suitable for a range of
industrial environments with low light levels, including railways, quarries, ports, and construction sites.
Identifying potential hazards in the workplace
Identifying hazards in the workplace is the most effective way of preventing them. A detailed risk assessment will help you establish the risks and put plans in place to prevent them. Risk assessments can include general assessments for the workplace (such as general office safety) but can also be for more specific projects or locations. A risk assessment should identify all risks, like the hazards at work examples above, and detailed mitigations to limit the risk. These risk assessments should be reviewed regularly to ensure all known risks and hazards are identified.
Maintaining health and safety is everyone’s responsibility. This is why, as an employer, you should take steps to provide the relevant health and safety training to your teams, while also ensuring you have responsible and trained individuals to conduct risk assessments. All employees should be given the right health and safety equipment and apparel to do their jobs without risk of injury.
Preventing hazards with phs Besafe
At phs Besafe, we supply businesses across a range of industries with protective workwear to help reduce potential hazards in the workplace. We sell Bright Gear, Foul Gear and Flame Gear, each with their own benefits to keeping your employees safe. We even offer a laundry service to help you keep your garments clean and maintained.
By taking steps to identify and prevent hazards in the workplace, you can fulfil your duties as an employer in protecting your employees.
Contact us today to find out more about our range of protective workwear.