LOLER 1998 Made Simple: Your Essential Guide to Lifting Operations and Equipment
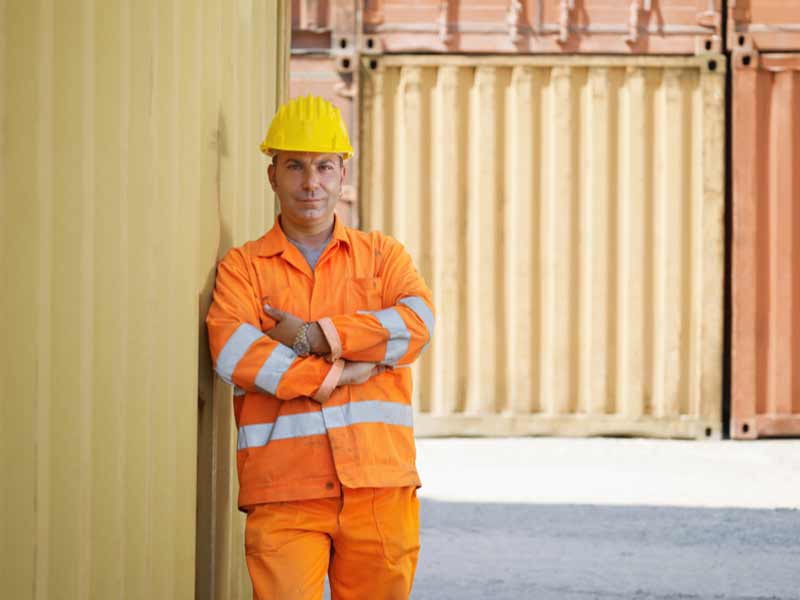
If your business involves lifting people or loads,
understanding your legal responsibilities is essential. The Lifting Operations
and Lifting Equipment Regulations 1998 - commonly known as LOLER 1998 - are
designed to ensure lifting equipment is used safely in the workplace. But what
is the Lifting Operations and Lifting Equipment Regulations 1998 really about,
and how can your business stay compliant?
Read our latest blog that can help break it down to help you
uunderstand your obligations and avoid costly mistakes.
What is LOLER 1998?
LOLER 1998 stands for the Lifting
Operations and Lifting Equipment Regulations 1998. Introduced under the Health
and Safety at Work Act, it sets out the rules for using lifting equipment
safely in all workplaces. The regulations apply to any equipment used at work
for lifting or lowering loads, including accessories and attachments.
So, what are the Lifting Operations and Lifting Equipment Regulations
1998? Put simply, it’s the legal framework ensuring that lifting operations are
properly planned, supervised, and carried out safely.
Why is LOLER important?
Failure to comply with LOLER can lead to serious workplace
accidents, injuries, fines or even prosecution. These regulations are in place
to:
- Protect
workers and the public
- Minimise
risk of equipment failure
- Promote
planned, risk-assessed lifting procedures
- Support
a culture of safety in the workplace
LOLER also helps businesses remain compliant with UK health
and safety law, making it an essential part of operational planning.
Who does LOLER apply to?
LOLER applies to any business or organisation that uses
lifting equipment, regardless of size or industry. This includes:
- Employers
- Self-employed
individuals
- People
or organisations responsible for equipment control (duty holders)
Whether you own the equipment or hire it in, if you control its use then lifting operations and lifting equipment regulations apply to you.
Examples of lifting equipment and industries that use it
Lifting equipment specifically falls under the scope of
which regulations? That’s right - LOLER 1998.
Common lifting equipment includes:
- Cranes
- Forklift
trucks
- Mobile
elevating work platforms (MEWPs)
- Vehicle
lifts
- Hoists
- Lifting
accessories like chains, slings, and shackles
Meanwhile, the industries where LOLER applies include:
- Construction
- Manufacturing
- Warehousing
and logistics
- Healthcare
- Agriculture
- Waste
management
Key duties for employers and workers under LOLER
Under LOLER, employers and duty holders are required to:
- Ensure
lifting equipment is strong, stable, and suitable for its intended use
- Properly
mark equipment with safe working loads (SWLs)
- Ensure
all lifting operations are planned and carried out by competent people
- Schedule
regular inspections and maintenance
- Keep
accurate records of all equipment examinations
Employees also have responsibilities, such as using
equipment correctly and reporting any faults or concerns.
How to plan safe lifting operations
Safe lifting isn’t just about equipment. It’s about making
sure the job is done safely. Under LOLER, all lifting operations must be:
Properly planned
A competent person should plan each lifting task, taking
into account the load, environment, equipment, and personnel involved.
Appropriately supervised
Even the best plan needs careful oversight. Someone with the
right knowledge should supervise to ensure procedures are followed safely.
Carried out safely
All lifting tasks must be executed with care, using the
right equipment, following best practices, and avoiding unnecessary risks.
LOLER inspections - what you need to know
LOLER requires lifting equipment to be thoroughly examined
at specific intervals. Ensuring your business or organisation follows these
practices is crucial for health and safety management, so make sure you
familiarise yourself with key dates and procedures.
How often are inspections required?
- Every
6 months for lifting equipment used to lift people.
- Every
6 months for lifting accessories (e.g., slings, chains).
- Every
12 months for other lifting equipment (e.g., forklifts, cranes).
However, more frequent checks may be required depending on
usage and working conditions.
Who can carry out LOLER inspections?
A competent person-someone with the necessary knowledge,
experience, and independence must conduct the inspection. This could be an
in-house qualified engineer or an external inspection body.
Record keeping
You must keep detailed records of:
- All
inspections and examinations
- Any
defects found and actions taken
- Maintenance
and repair history
These records must be available for at least two years or
until the next inspection, whichever is longer.
The difference between LOLER and PUWER
While LOLER focuses specifically on lifting equipment, PUWER-the Provision and Use of Work Equipment Regulations 1998 applies to all work equipment.
The differences include:
Regulation | Focus | Applies
to |
LOLER | Safe lifting operations and lifting equipment | Equipment used for lifting loads or people |
PUWER | Safe use of all work equipment | All equipment used at work (including lifting gear) |
In many cases, both sets of regulations apply
simultaneously.
Staying compliant with LOLER
To stay compliant with LOLER, consider the following steps:
1. Identify
all lifting equipment in your workplace
2. Ensure
it's fit for purpose and regularly inspected
3. Train
staff on safe use and responsibilities
4. Keep
clear, up-to-date records
5. Use
competent people for planning and supervision
Being proactive about LOLER compliance reduces risks and
demonstrates your commitment to workplace safety.
Provide safe work equipment with phs Besafe
Keeping your lifting operations safe and compliant is easier when you partner with trusted experts. At phs Besafe, you can equip your workplace with everything it needs to maintain safety and keep workers safe on the job. We not only sell protective workwear garments, but we also provide laundering services for protective gear, helping you maintain a safe and efficient workwear environment.
No matter your industry, it’s always important to put safety first. Contact us today to find out more about our services and how we can become your trusted partner in maintaining workplace safety.